Stamping part manufacturing refers to the process of transforming metal sheets into parts of various shapes and sizes through stamping processes. This manufacturing process is widely used in industries such as automotive, aerospace, electronics, and home appliances. Its advantages include efficient production, low material consumption, and precise dimensional control.
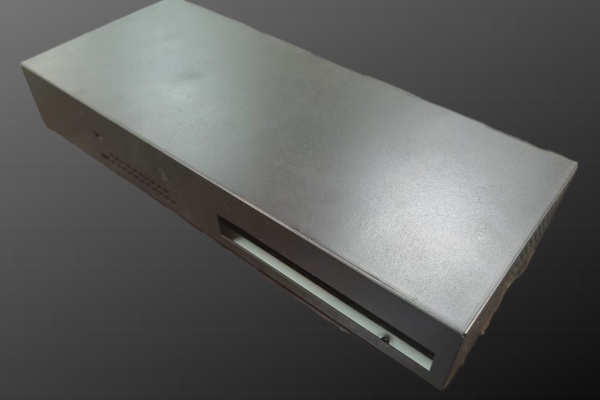
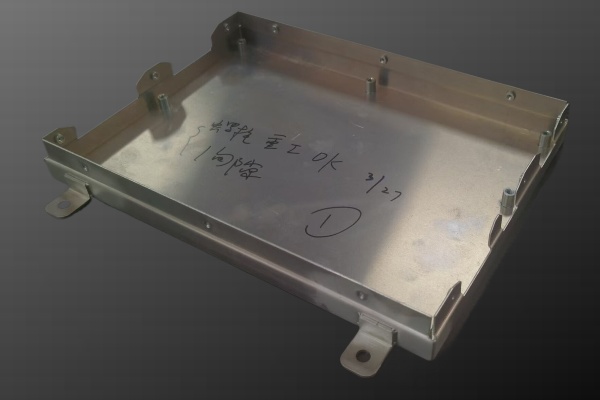
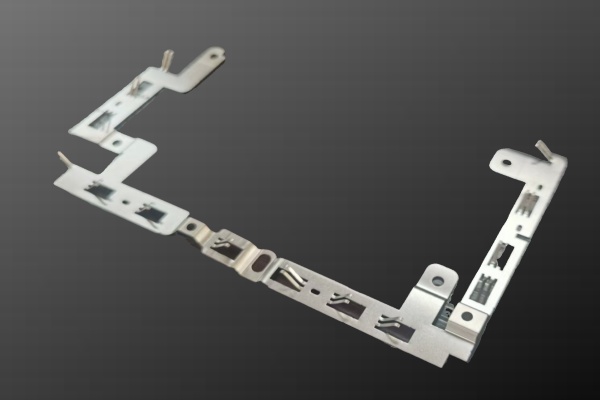
In the stamping process, a combination of a press and a die is typically used. First, an appropriate die is manufactured according to the design requirements of the product. Then, the metal sheet is placed on the press, where pressure is applied through the die, causing the metal sheet to be cut, bent, or formed into the desired shape. This process can be completed in a very short time, making it especially suitable for mass production.
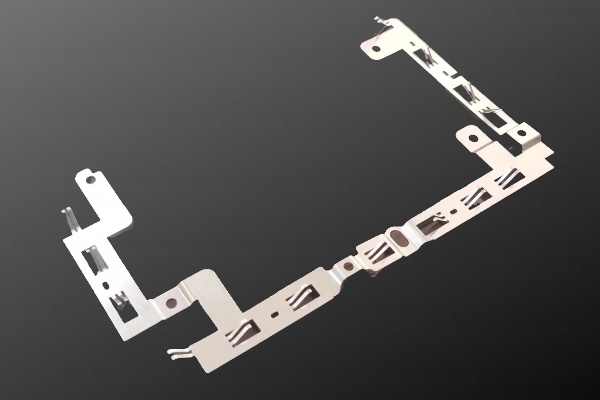
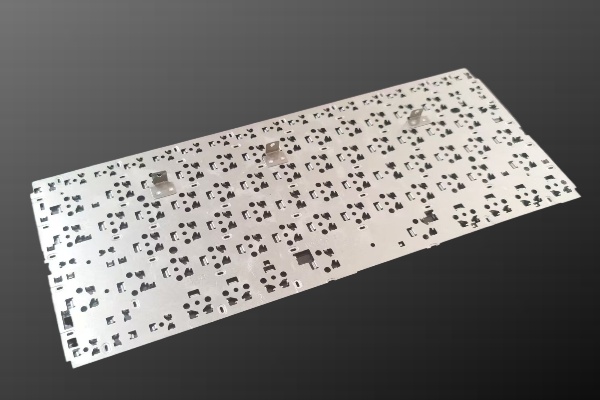
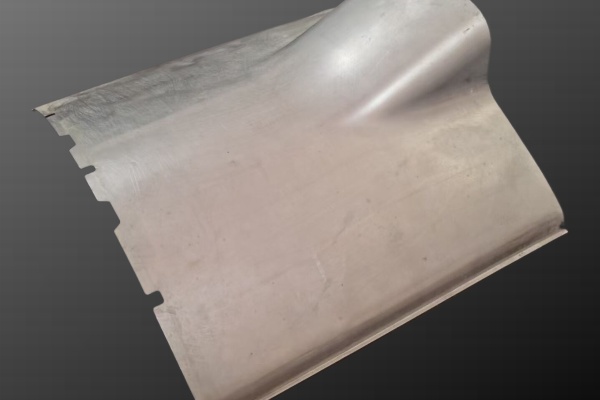
The selection of materials for stamped parts is crucial, with commonly used materials including stainless steel, aluminum alloys, and copper. Selecting appropriate materials can ensure the rigidity and durability of the product, while also reducing material waste and production costs. Manufacturers typically decide on material selection based on the product's application environment and performance requirements.
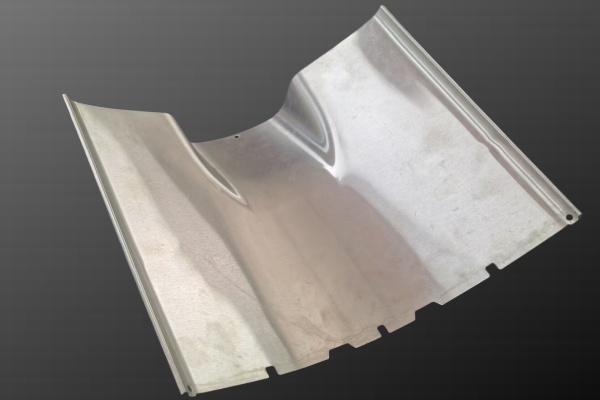
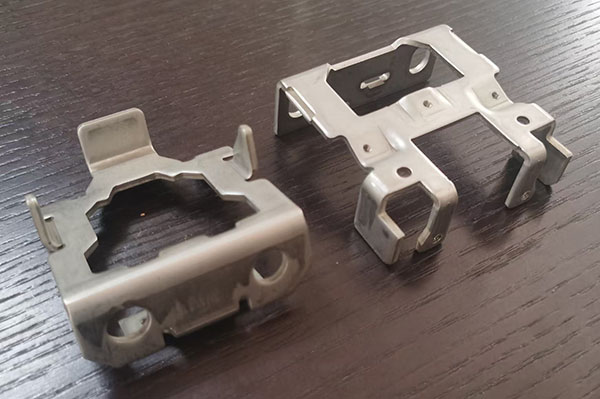
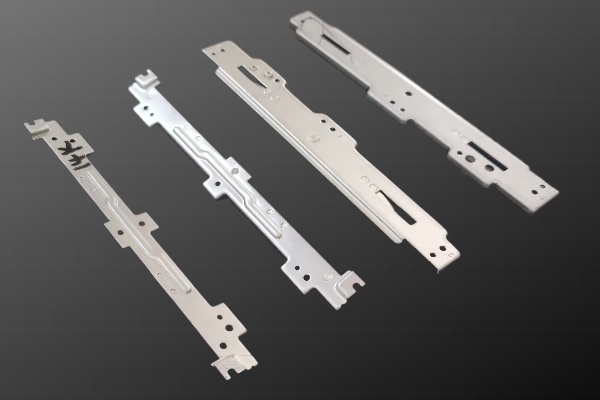
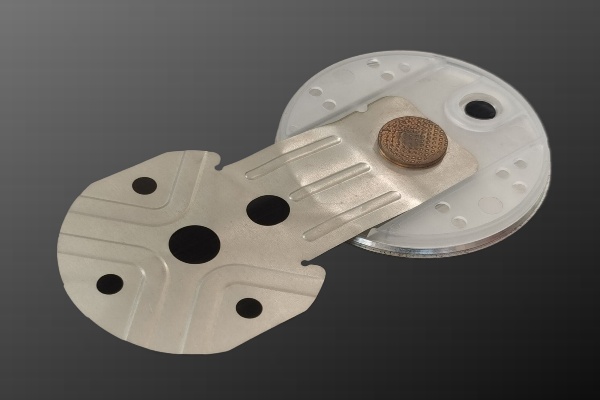
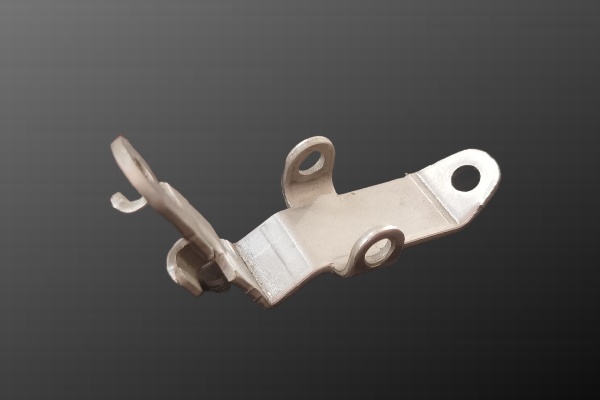
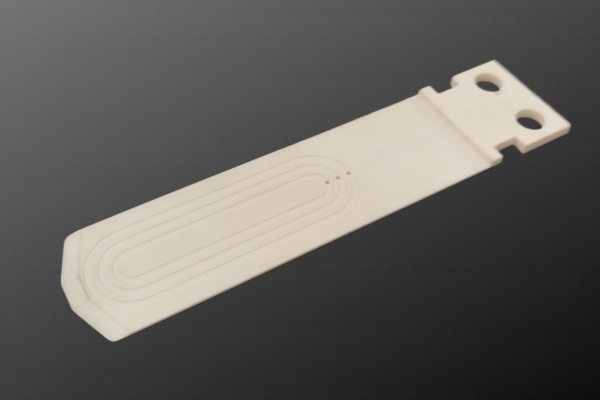
However, stamping part manufacturing also requires meticulous process management and quality control. The design and maintenance of the dies, precision calibration of the press, and monitoring of the production process are key factors in ensuring product quality. Additionally, effective management and recycling of scraps and offcuts generated during production are necessary to achieve green manufacturing.
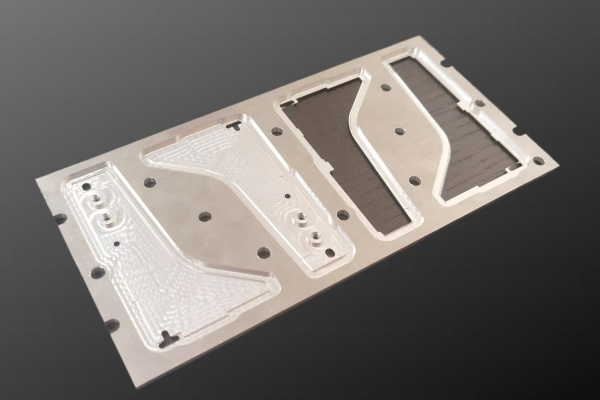
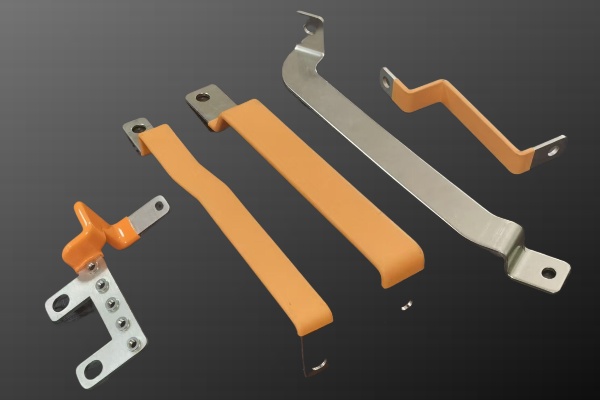
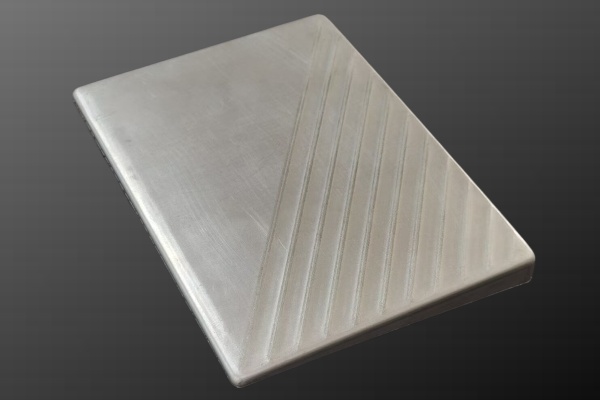
In summary, stamping part manufacturing is an efficient metal processing technology that holds an important position in modern industry. Understanding and mastering the process flows, material selection, and quality control aspects can help improve production efficiency and product quality, creating greater value for enterprises.
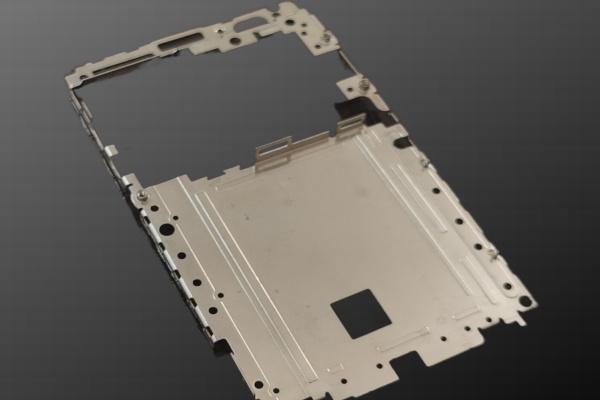
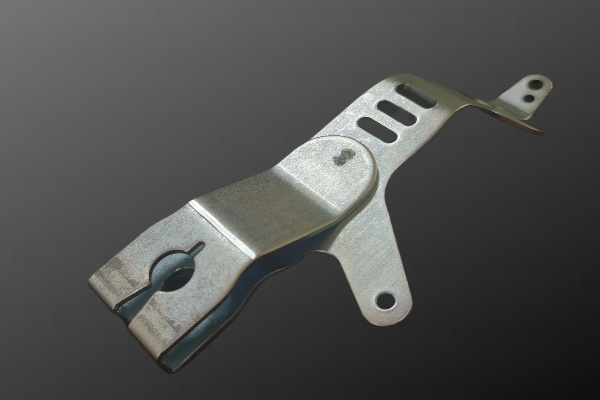
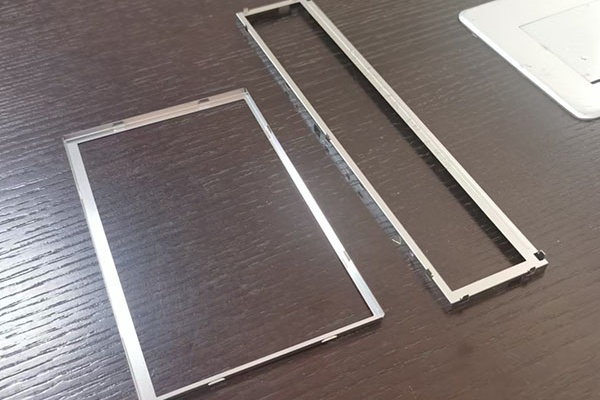
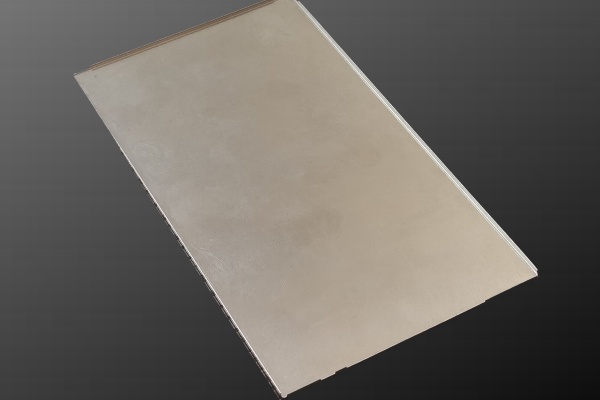
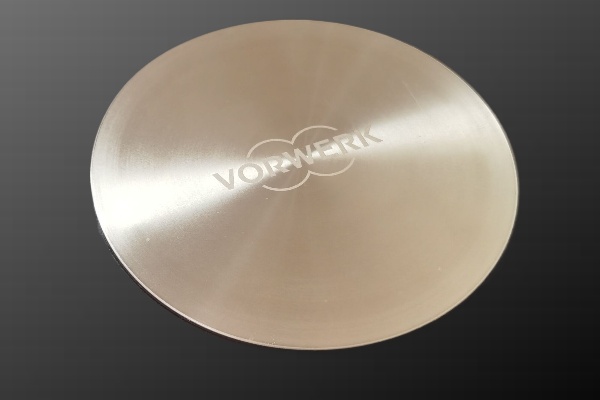
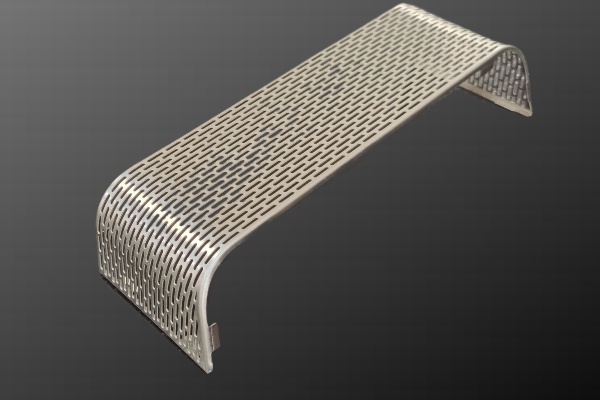
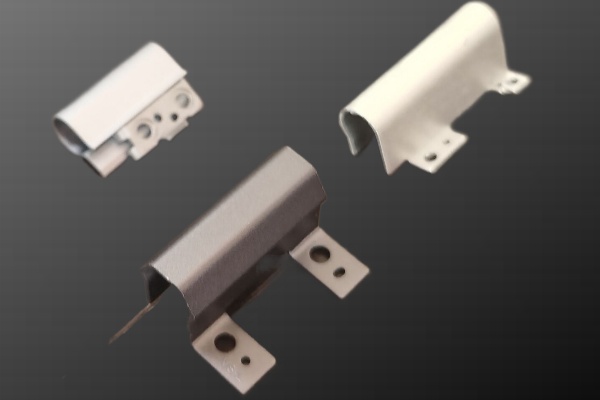
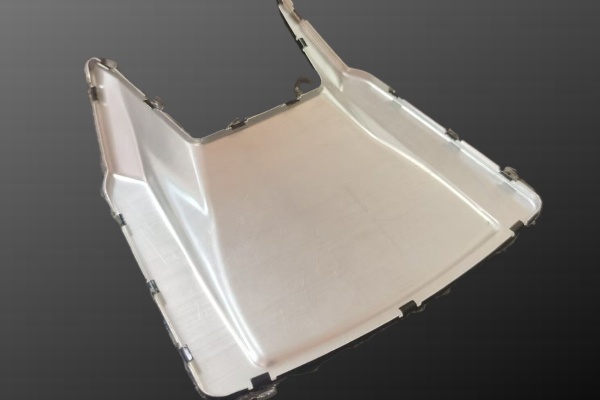
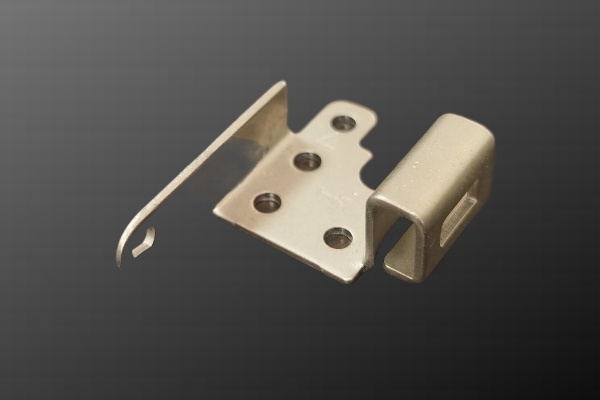
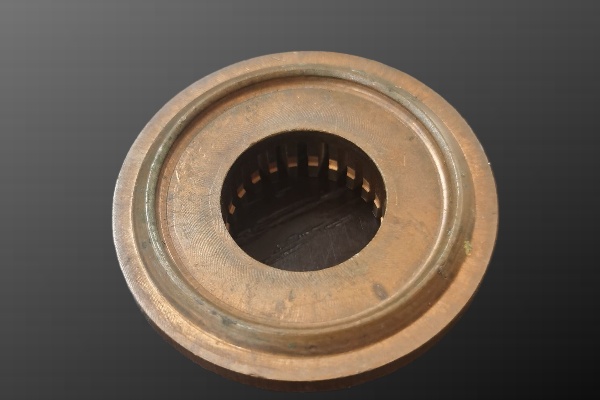
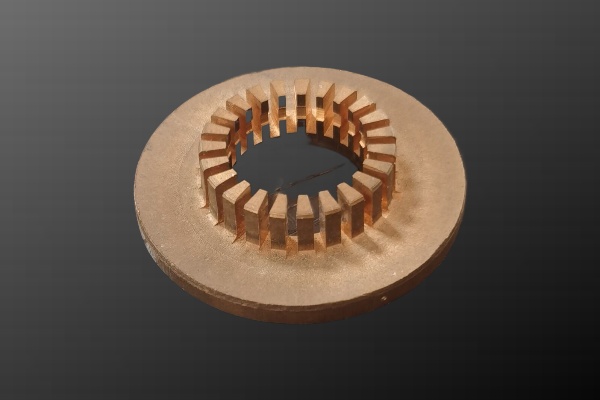
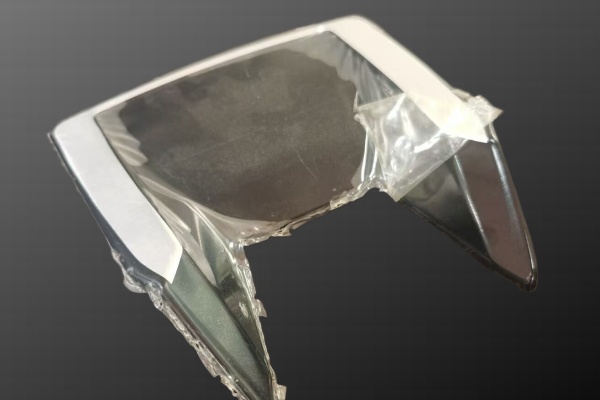

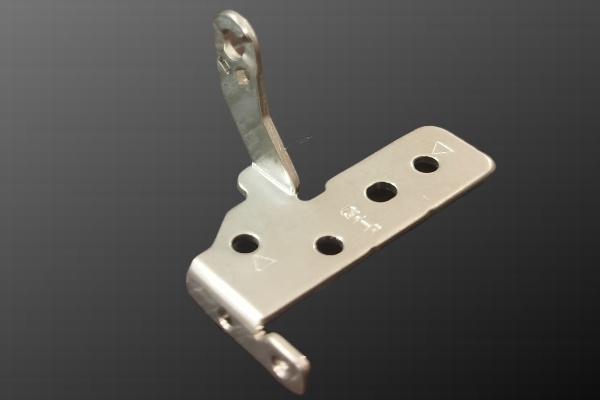

Post time: Oct-30-2024